Anti-Aging Solutions For Cement Plants And Tackling New Challenges Due To Refuse Derived Fuel.
Edited by Mark S. Kuhar
Fulfilling a large order may mean that a cement plant needs to keep running at full capacity over extended periods. This creates risk as major cracks and wear can develop in equipment.
Vladimir Filipov, key customer manager at repair specialist Remoterm, draws on his experience as an official Castolin Eutectic representative to explain what’s possible in terms of repair – and how maintenance can maximize profitability.
Cracks
Regular maintenance is essential for productivity. Issues such as crack and excessive wear develop due to heavy mechanical loads, high temperatures and a flow of corrosive and abrasive cement.
When it comes to cracks, these form and develop in the body of machinery such as kilns, mills and other equipment. Cracks initiate at tiny pre-existing defects in the body of cast or forged components but grow steadily over thousands of loading cycles as a kiln rotates.
Although cracks are almost invisible to the naked eye, they pose a critical risk to the health and safety of frontline workers, business continuity and the environment. If a crack is overseen, it will lengthen and deepen over time and will eventually affect the component’s structural integrity.
It could experience sudden catastrophic failure, which would be a major threat for worker safety, as well as requiring a lengthy plant shutdown for repair or even a complete replacement of the affected hardware.
This makes the identification and repair of cracks essential, particularly in critical equipment such as the tires, girth gears and bodies of kilns. In Filipov’s experience, kiln tires are the single most common type of repair at cement plants – and being process-critical, cracking cannot be overlooked.
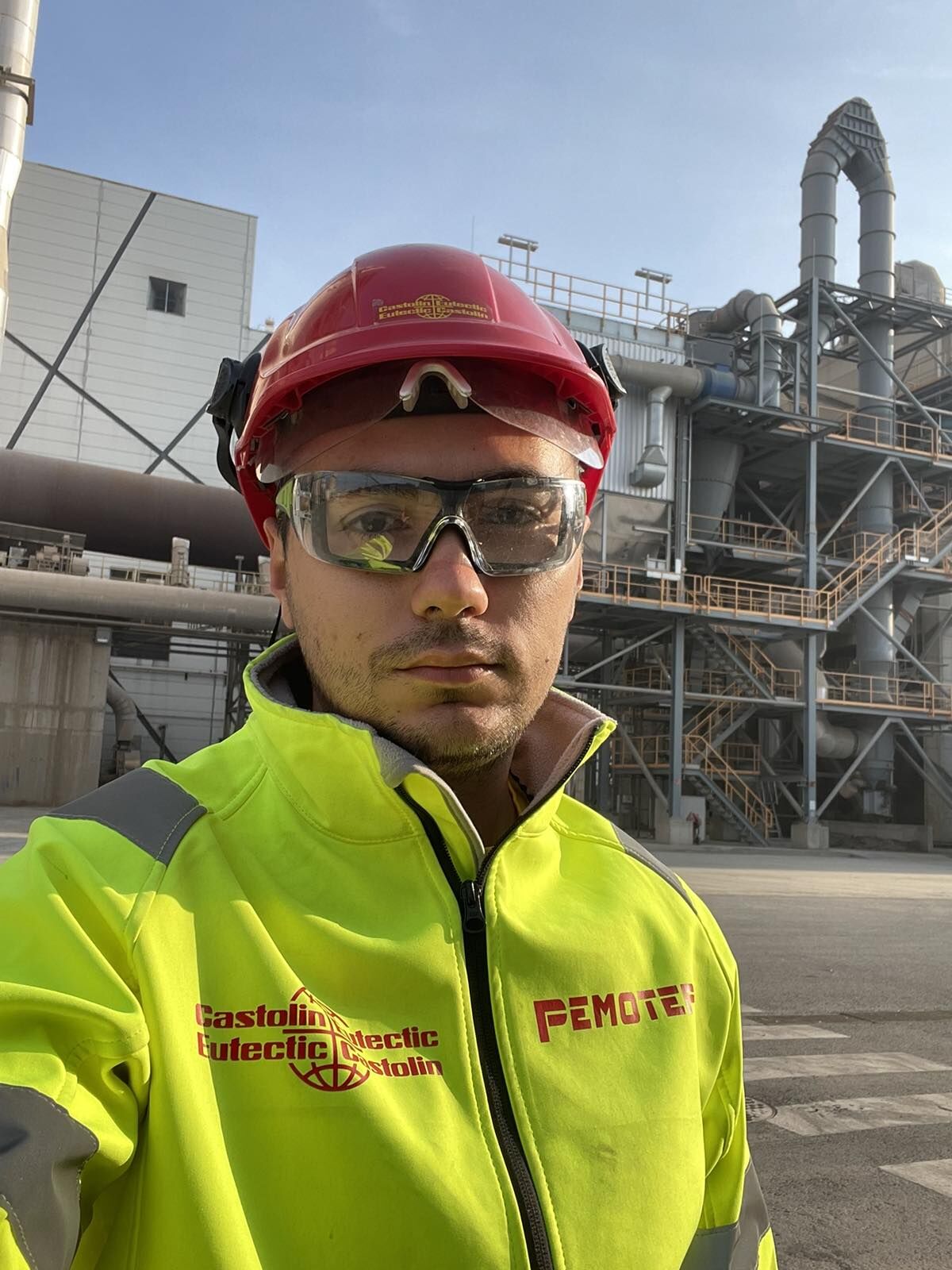
Excessive Wear
It’s a similar picture with excessive wear. Components in crushers, vertical roller mills (VRMs), ball mills, pneumatic systems and transport screws all experience wear due to the constant flow of cement. This impacts equipment efficiency and lifetime. We are regularly called in to apply hardfacing coatings to such as grinding rollers and tables, as well as crusher teeth and bars.
“Overall, around one third of our business comes from the cement industry and we have travelled as far afield as Brazil,” Filipov said.
The Dilemma: Keep Production Going vs. Repair at Peak Times
Plant managers need to balance the value of a short outage at peak production time versus a longer one over the winter. This becomes trickier when construction is booming and demand is high.
Remoterm has been finding itself in high demand during 2023 due to a large number of building projects in its market areas. This has driven up demand for cement and caused more stress on production.
In order to avoid lost production time, plant managers typically plan shutdowns over the winter period. They take equipment out of service and conduct repairs when orders are low. The challenge is that this can “save up” problems from growth of cracks and wear over the peak production period, creating the need for larger and more costly repairs and longer outages.
When an operator is under pressure to meet contractual obligations, they sometimes take the risk to return the equipment to service without a repair. And the longer it remains in service, the more the crack will grow. It is a difficult decision between short-term gain and longer-term pain.
On one occasion, we repaired a crack that had grown to a length of one meter after the operator left it in service for a month to meet an order backlog. “We’ve also repaired many cracks of around 250 mm,” Filipov stated.
Strategic Investment in Non-Destructive Testing
The most important defense against cracks is to be aware of them. “Therefore, we recommend non-destructive testing (NDT) based on magnetics or dye penetration,” Filipov said. This enables the cement operator to identify the location and extent of cracks. “We’re usually called in to repair cracks of 50 mm or more in length. They are fairly straightforward to repair in a matter of days but if left, may grow fast.”
“Around half of our projects are based on unplanned emergency repairs. That shows that many operators are not using NDT to identify cracks and plan repairs,” added Filipov.
“Emergency repairs are good business for us as they come at a cost premium and tend to be larger and last longer than planned projects,” Filipov stated. “However, they are unpredictable and require our technicians to travel away from their families urgently for extended periods. Therefore, we always recommend that cement operators invest in NDT so that they identify cracks in equipment and know what level of risks they’re facing. This will cut the cost of repair work by limiting the size of repairs and it will enable us to plan our resources more effectively.”
The best way to carry out NDT is to put systems in place for regular testing. It will require short outages on kilns but it’s often possible to take a mill or crusher out of service on one line while another line stays in service.
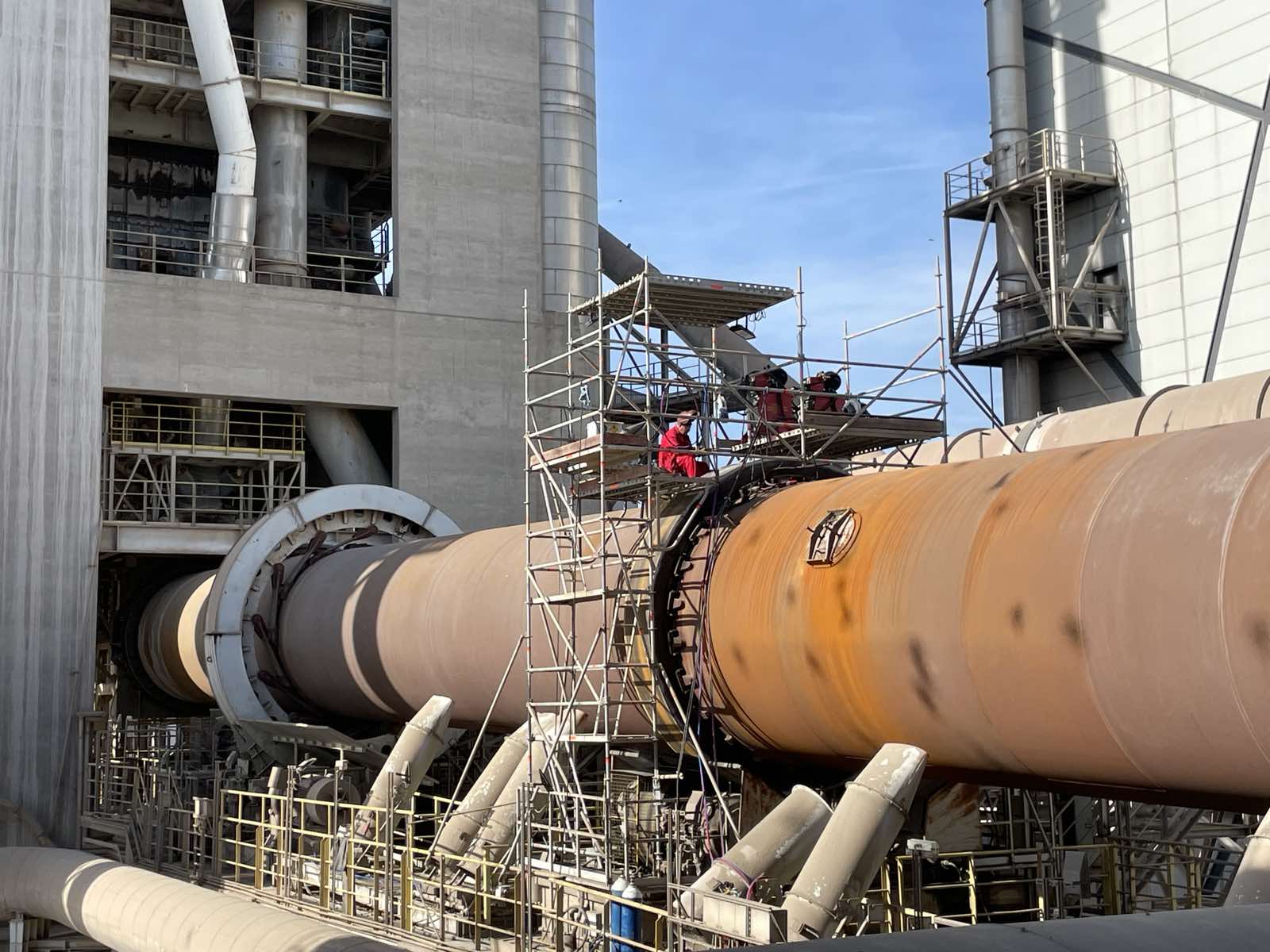
Round-the-Clock On-Site Intervention
During repair, cracks need to be completely removed as a first step. If even a tiny imperfection is left, it will act as a stress raiser and will become a site for a new crack to initiate.
“To prevent this, we have a methodology in place,” Filipov said. “It starts with inspection and goes on to cleaning and chamfering to completely remove the crack to its full depth and length. We then go on to welding and reinforcement using a welding consumable with a very high tensile strength of more than 7,800 Newtons per millimeter. It can also withstand more than 45 % elongation. After this, a final post-weld heat treatment avoids stress build-up inside the component.
“The technique requires continuous working, with three shifts over a 24-hour day to maintain continuity in the material. We also using cooling to limit deformation of the base material, protect it from thermal shock. This maintains its original dimensions, which can be a critical factor in machine operation.
“Our largest-ever repair at a cement plant was in the body of a ball mill. Although the equipment was less than four years old, there were defects in the material. A crack had initiated and eventually grown to a length of 3.5 meters. We completed the repair over two months on a 24/7 basis.”
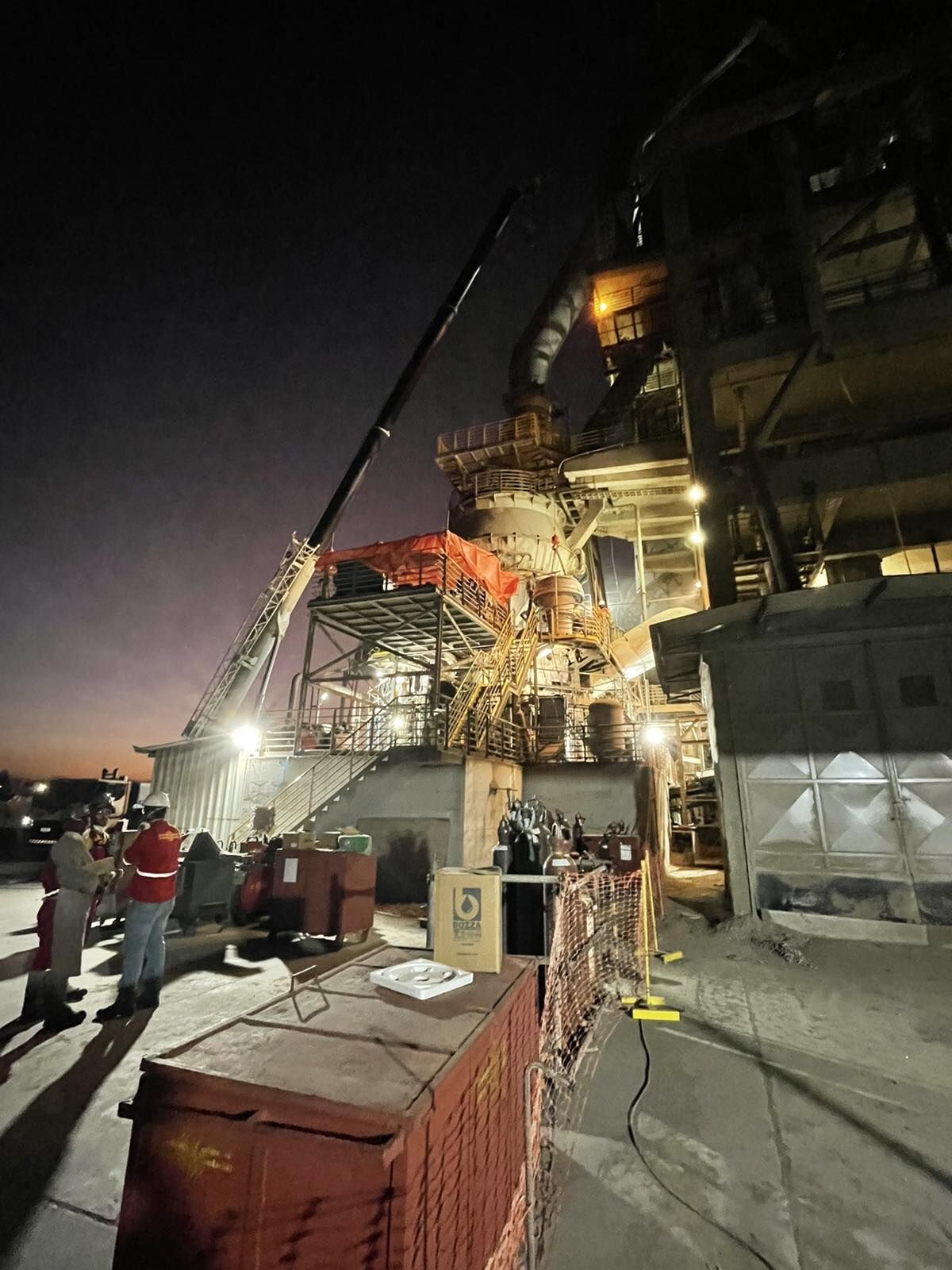
Challenges Due to Refuse Derived Fuel (RDF)
A new trend that’s influencing maintenance schedules at cement plants is the growing use of refuse derived fuel (RDF) instead of coal. It is more environmentally sustainable and also provides an income as cement plants earn a fee for accepting waste, whereas they need to pay for coal.
“We’re seeing that cement plants in Bulgaria, where we’re based, have switched to 70-85% RDF,” Filipov said.
The downside is that RDF is having an impact on plant reliability and maintenance as its content can vary widely. RDF may contain metal, rubber, plastics, paper, glass and kitchen waste. This affects its calorific value. In some cases, it also requires shredding before it can be used as fuel and that also creates maintenance requirements for the shredder.
The variability creates issues in the kiln due to inconsistent combustion, with temperatures that vary and can lead to the formation of cracks – and a need for more repairs.
“RDF can also cause excessive wear on pneumatic lines that transfer the fuel into the kiln. This is particularly true on pipe elbows, where fast-moving abrasive materials in the fuel wear away the interior of the lines. We’re seeing pipe elbows lasting less than two years,” Filipov said.
“This can be resolve by upgrading pipe elbows. Rather than using standard pipe fittings, it’s possible to source alternative versions with an ultra-hard internal coating in a material such as tungsten carbide. It’s extremely high hardness of 60-62 on the Rockwell hardness scale will resist wear and significantly extend the service life. We installed our first examples in 2016 and they’re still in service now, showing that it’s possible to achieve at least 2-3 times more service life than a standard fitting,” Filipov said.
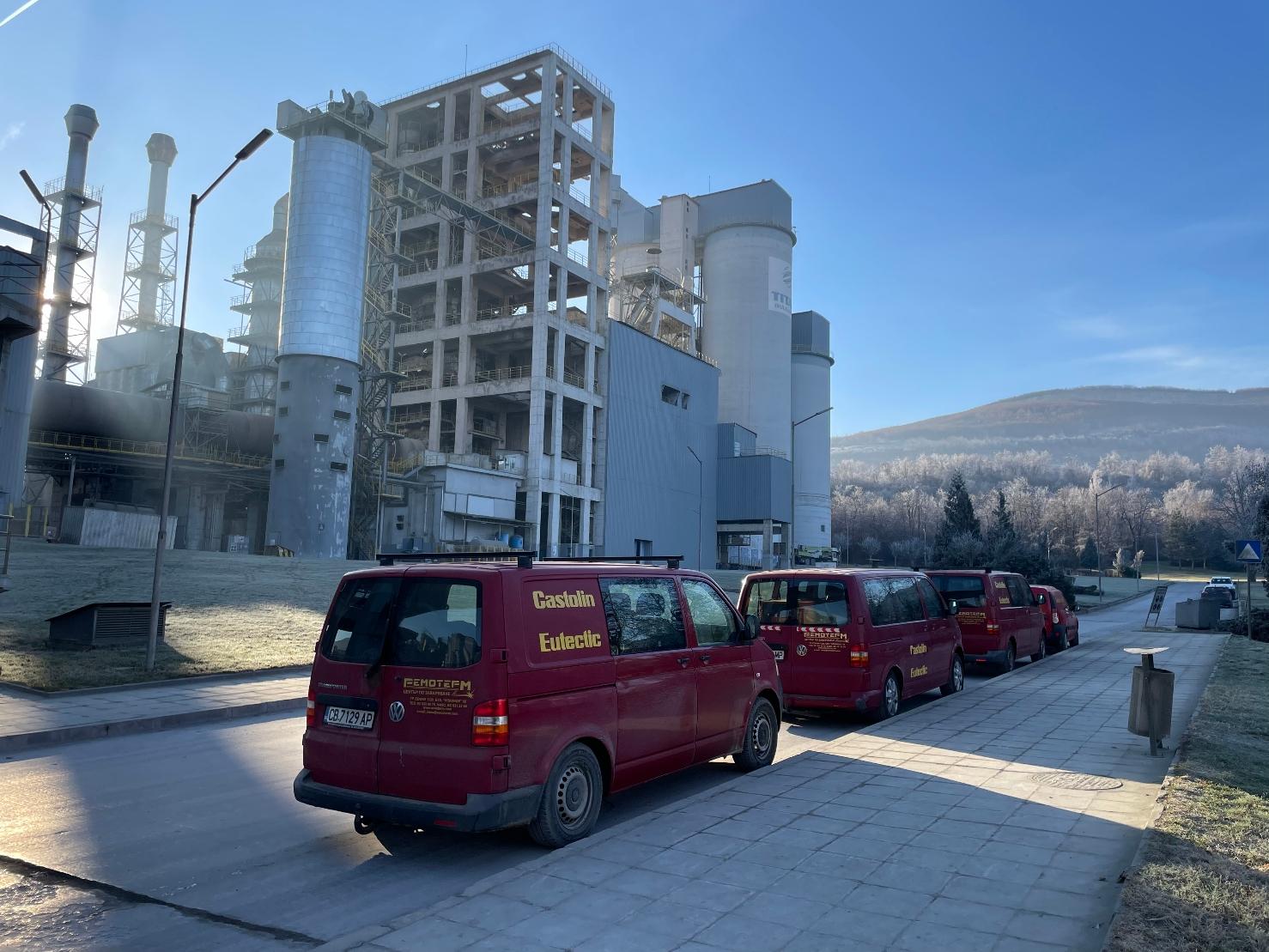
Achieving a Balance
It’s tempting to keep a cement plant running to meet short-term targets but it may come at a much higher cost further down the line. Cement plant operators face the challenge of finding a balance between losing a small amount uptime when demand is high, versus long outages over winter.
A proactive approach to NDT and maintenance will enable operators to evaluate the risks they’re facing and control the extent and duration of repairs. And when cracks grow very large, it’s useful to know that it’s often possible to make a repair and extend the lifetime of critical components.
Information for this article courtesy of Castolin Eutectic.